FIBER LASER CUTTING
CLEAN, ACCURATE, OXIDE FREE
WHAT IS FIBER LASER CUTTING
Fiber laser cutting is laser cutting using the latest generation of industrial lasers, which are Fiber Lasers. A fiber laser uses optical fibers as the active medium in the laser resonator. Fiber laser cutting offers unprecedented speed and accuracy and is a non-contact process that does not involve any physical grinding or milling which impose vibrations, stress, and friction into the material. Our specialized system uses a small spot size, .003” diameter, and advanced pulsing options, which result in a minimal heat-affected zones (HAZ) and low overall temperature conducted into the workpiece.
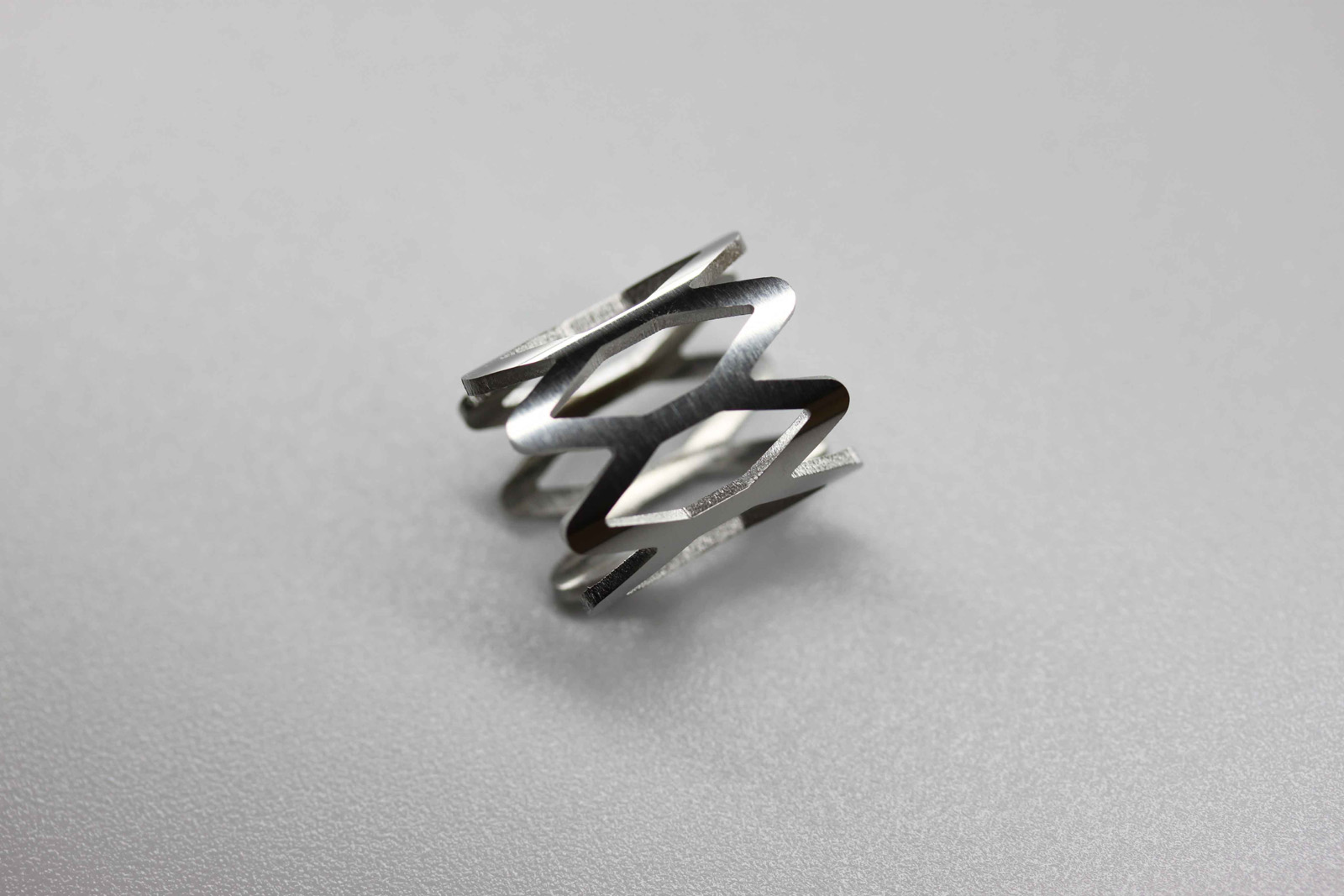
OUR FIBER CUTTING CAPABILITIES
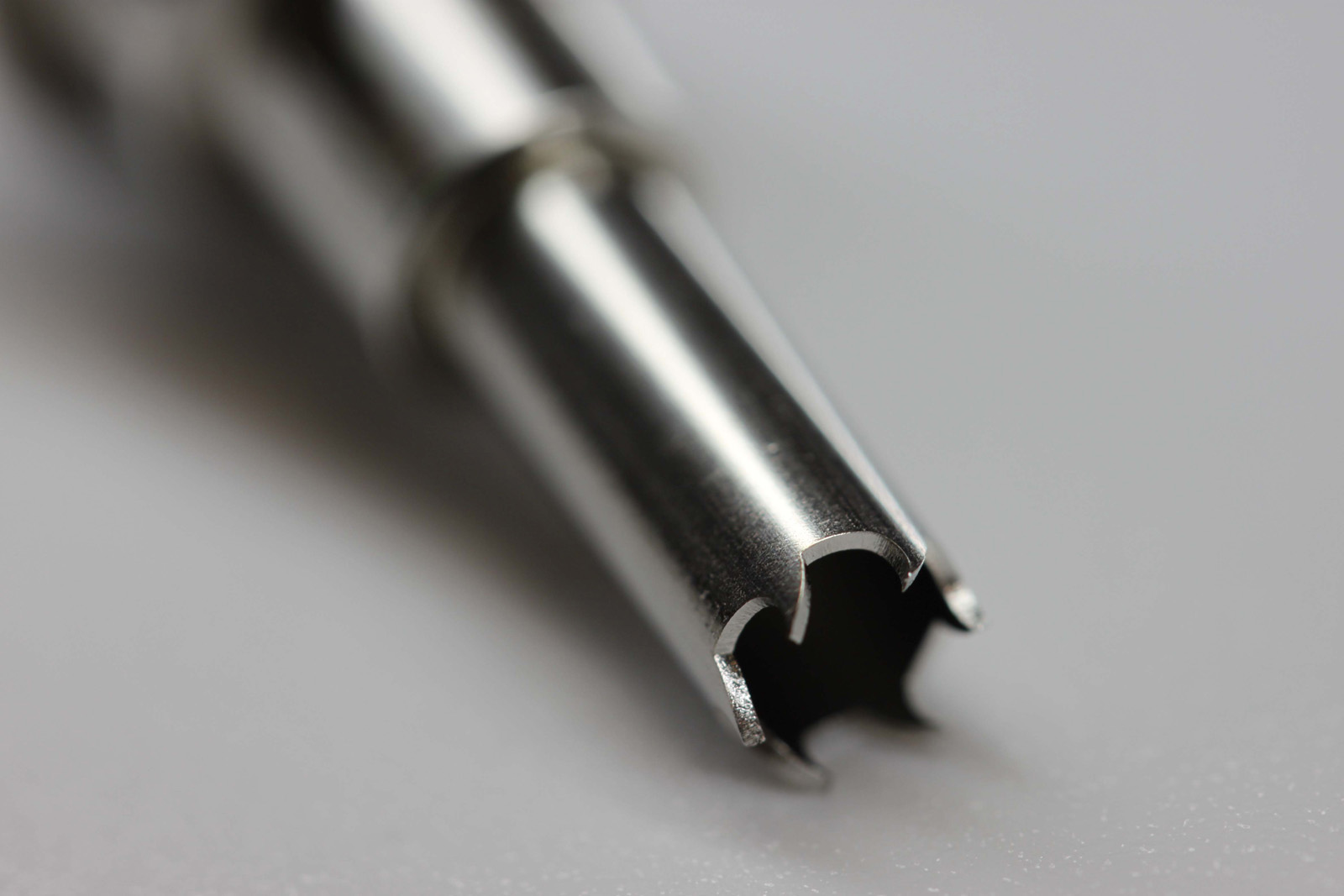
- Materials
- Mild Steels
- Low carbon Steels; Stainless & alloys
- Aluminum
- Brass
- Silicon
- Thicknesses
- Mild Steel – 5mm max thickness
- Stainless – 2.5 mm max thickness
- Aluminum – 2 mm max thickness
- Brass – 1 mm max thickness
- Maximum part dimensions
- 11.8” [300mm] square (flat stock)
- 3” diameter (tubing)
THE FIBER LASER CUTTING PROCESS
There are two main processes in Laser Cutting:
- oxide free edge cutting which uses an inert assist gas such as Nitrogen
- reactive cutting which uses a reactive assist gas such as Oxygen
In Laser cutting, the cut width (known as kerf) that is produced is the same width as that of the focused laser beam. When the focused laser beam hits the workpiece, the material heats up to the extent that it is liquified and vaporized. A pressurized gas source is used to improve the cutting process by pushing the vaporized and liquefied material out through the kerf.
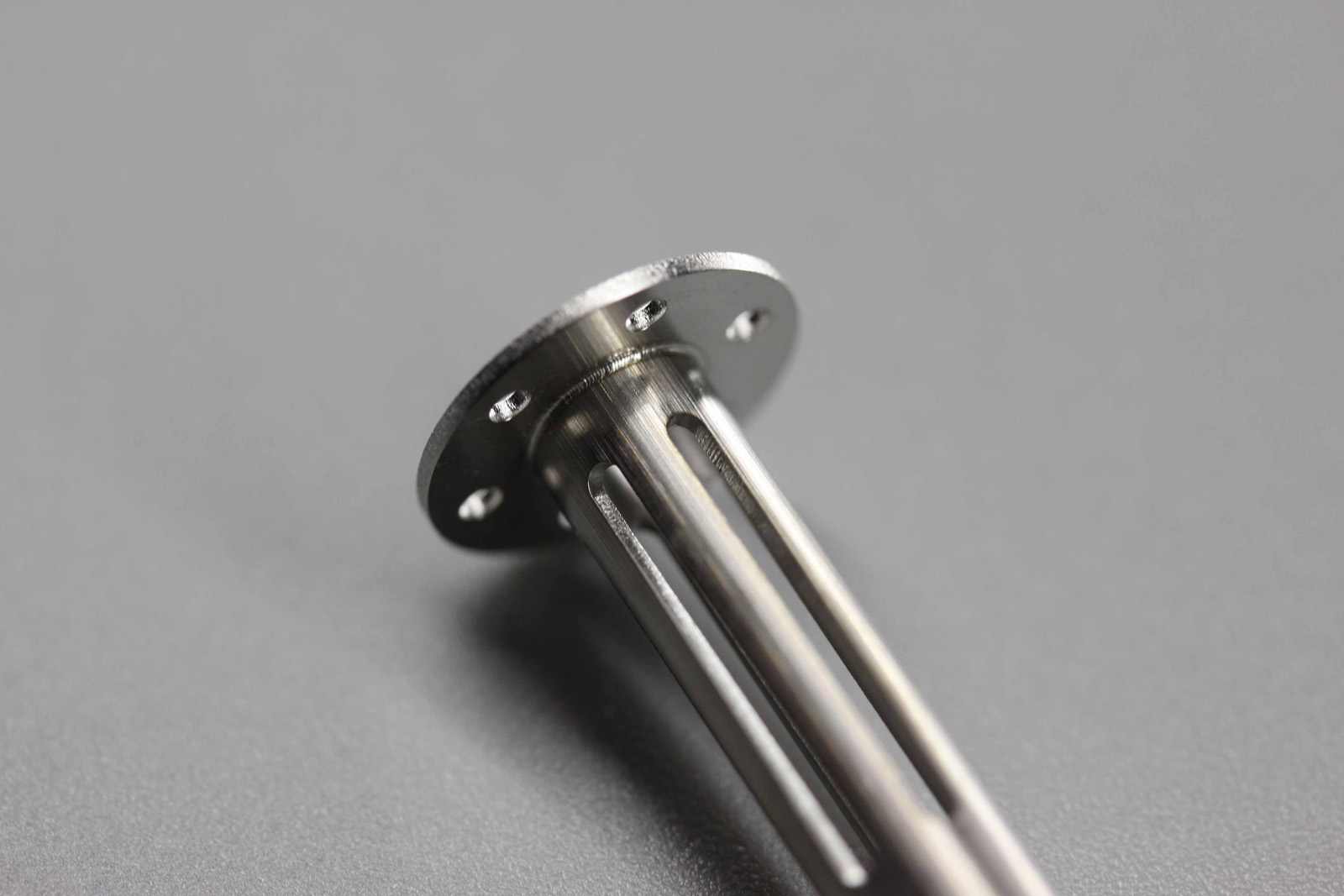
BENEFITS/ADVANTAGES OF FIBER LASER CUTTING
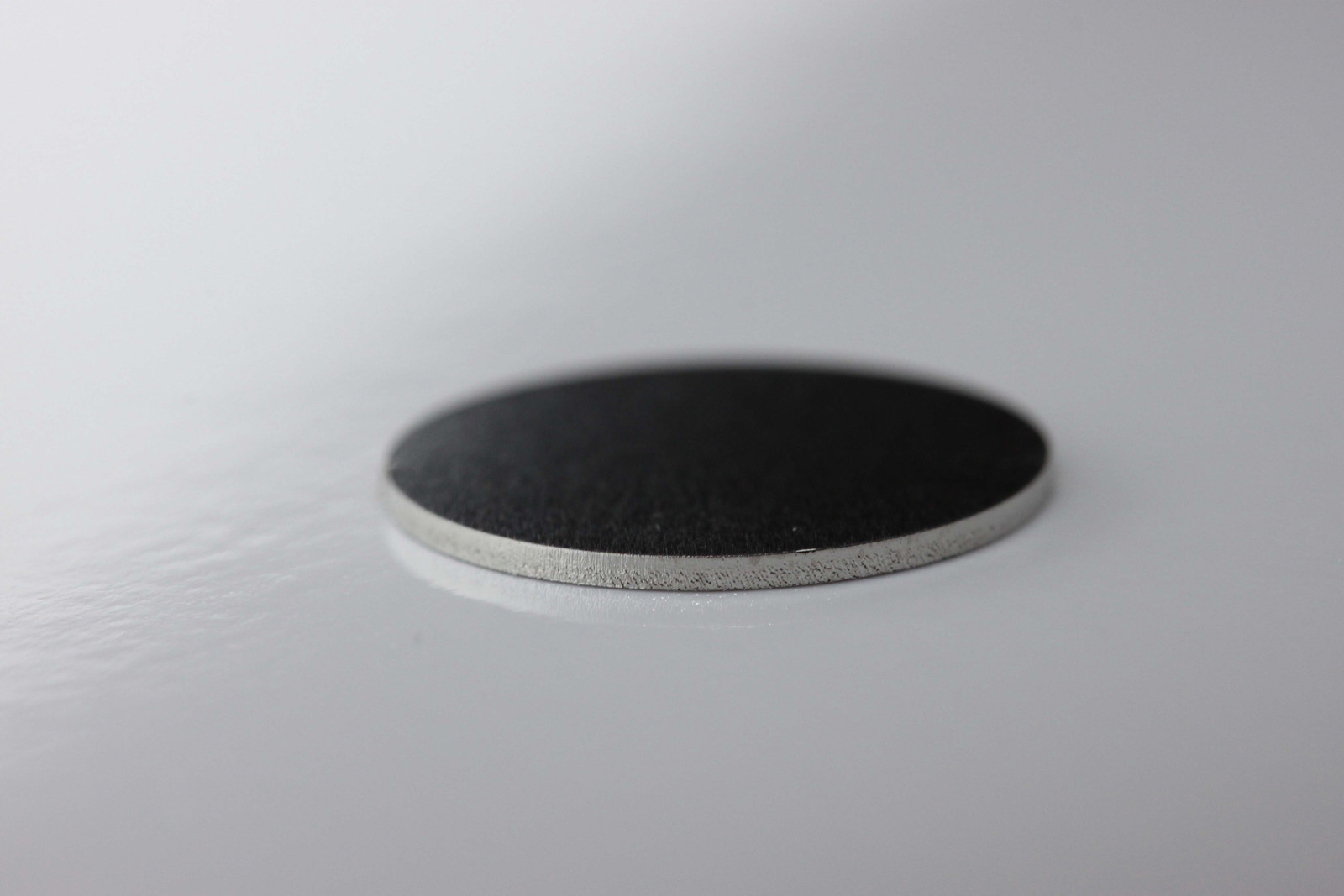
Lower powered fiber lasers (500 Watts and under) are often air cooled with fans and do not require water cooling. These lasers have many advantages like power stability, high reliability, compact footprint, excellent beam quality, electrical efficiency, and low maintenance costs.
Fiber Laser cutting is the go-to technology to perform cutting jobs in the industry because of these advantages.
- Cuts non-ferrous materials with ease
- Cuts complex and intricate shapes with precise detail
- Non-contact, non-wearing for continuous part repeatability
- Excellent oxide free edge finish when using an inert assist gas