QUALITY ASSURANCE
3 STEP QUALITY INSPECTION PROCESS
QUALITY ASSURANCE
Here at Laser Dynamics, we believe that quality is the cornerstone of a good business model and strive to ensure that only the highest quality parts leave our facility. Laser Dynamics uses a 3-part quality inspection process when working with our customer’s products. These three steps are pre-process, in-process and post-process and they ensure that we produce only high-quality products for our customers.
PRE-PROCESS INSPECTION
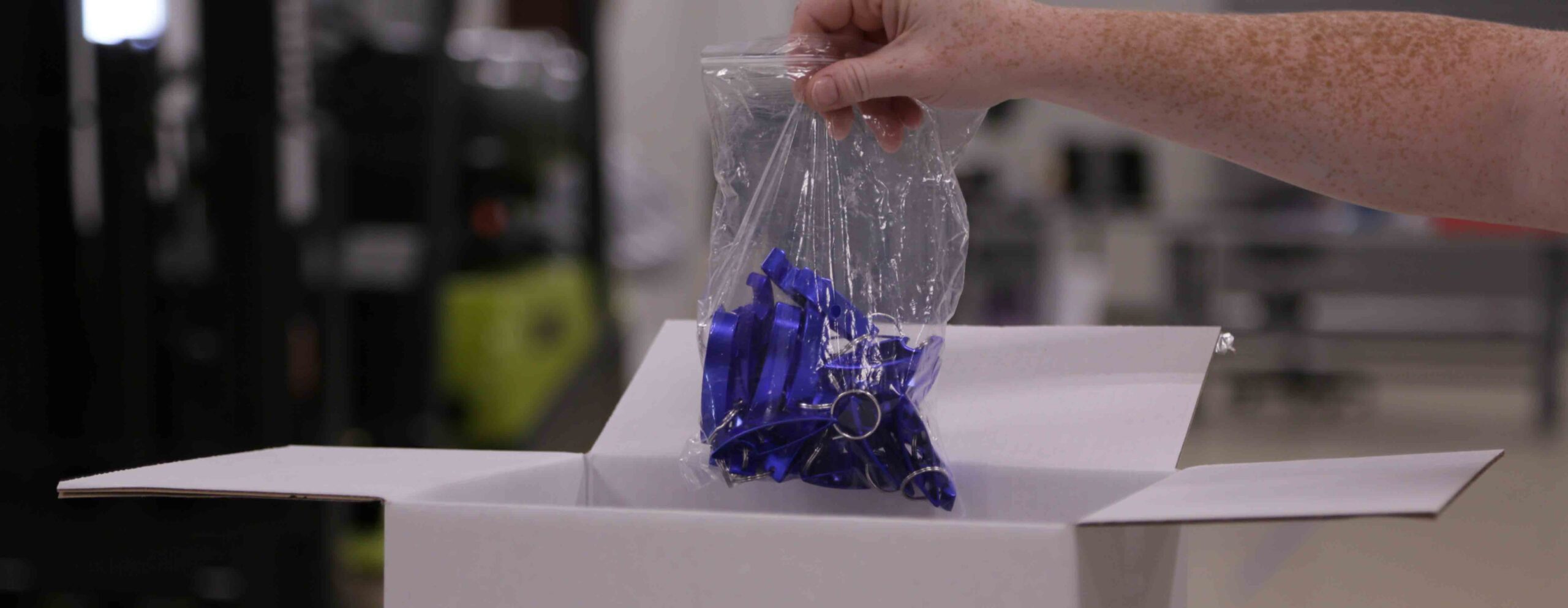
Once an order is received and documented, our receiving specialist matches the parts to the purchase order and assembles all additional materials related to the order including the manufacturing drawing. From this point on our customer’s parts are married to the correct documentation throughout their journey while in our facility. This ensures lot-integrity throughout receiving, production, quality control, and finally, order fulfillment.
IN-PROCESS INSPECTION
Our inspection capabilities include the use of state-of-the-art equipment to ensure that our products exceed even the most rigorous quality standards. Each product produced in our facility is lot sampled and undergoes quality assurance testing using a zero-based acceptance sampling plan, which ensures that the product dimensions are within specified tolerances. Additionally, our customers parts are 100% visually inspected for defects during production.
We use an AQL (Acceptable Quality Level) chart, which tells us how many parts need to be measured based on the lot size being processed. The AQL level to be used is established during the initial run of each product by our engineering and quality control teams. It is derived by measuring the performance of production variables using sigma-level metrics.
Irrespective of the sigma level of a particular manufacturing process, the important thing is that all rejects produced in the process are found and identified as non-conforming product and are not allowed to leave our facility labeled as conforming product. We are very proud to have consistently maintained our impeccable track record when it comes to quality control.
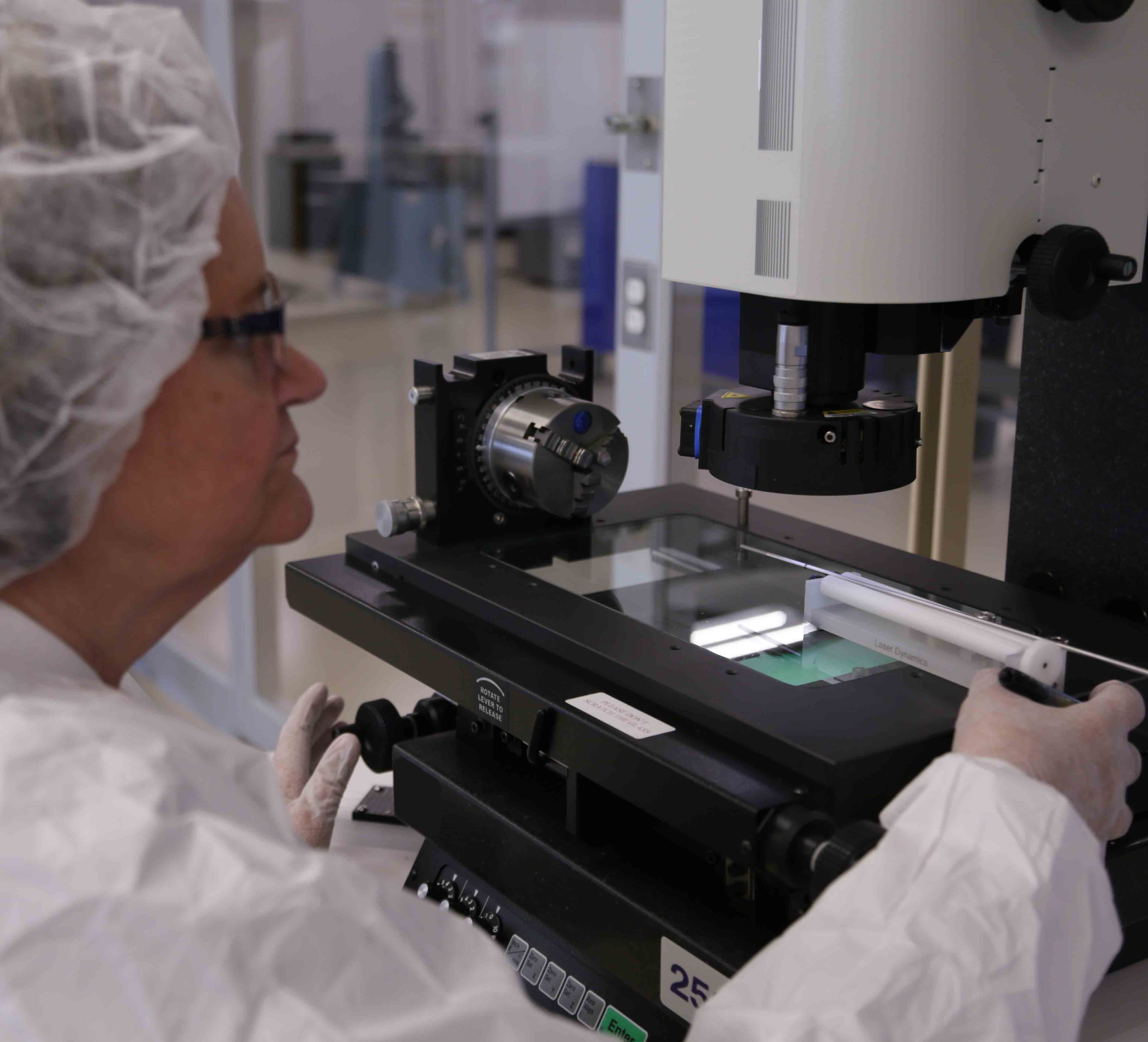
POST-PROCESS INSPECTION
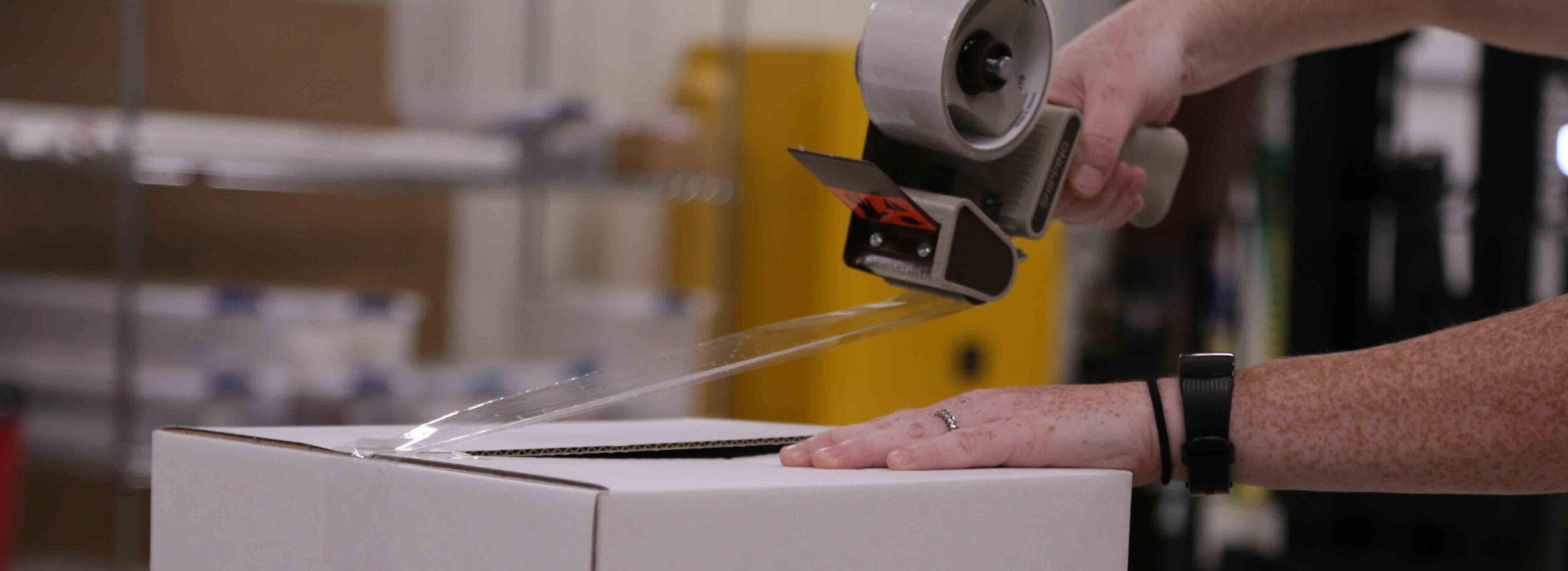
At this point, the paper-work is verified by our order specialist to ensure that all documentation has been recorded correctly. Once the paperwork has been verified, the parts are returned to our shipping department to be pre-packaged in their original containers and shipped to our esteemed customers. All of our packages are securely taped to ensure a safe journey for our customers’ products.