CORROSION RESISTANT BLACK MARKING ON STAINLESS STEEL
(and other metals)
WHAT IS BLACK MARKING?
Black Marking is a new laser marking technology that can eliminate the need for the passivation of stainless-steel medical parts after laser marking has been performed. Black Marked stainless steel parts can withstand hundreds of autoclave cycles without signs of corrosion without having to passivate the parts after laser marking. Black Marking also appears darker than traditional laser markings. Black Marking is done with lasers that can achieve pulse durations that are extremely short and can be set to as low as 350 femtoseconds in length. To put that in perspective, 1 femtosecond is equal to one millionth of one billionth of a second or one quadrillionth of one second, a very short laser pulse indeed.
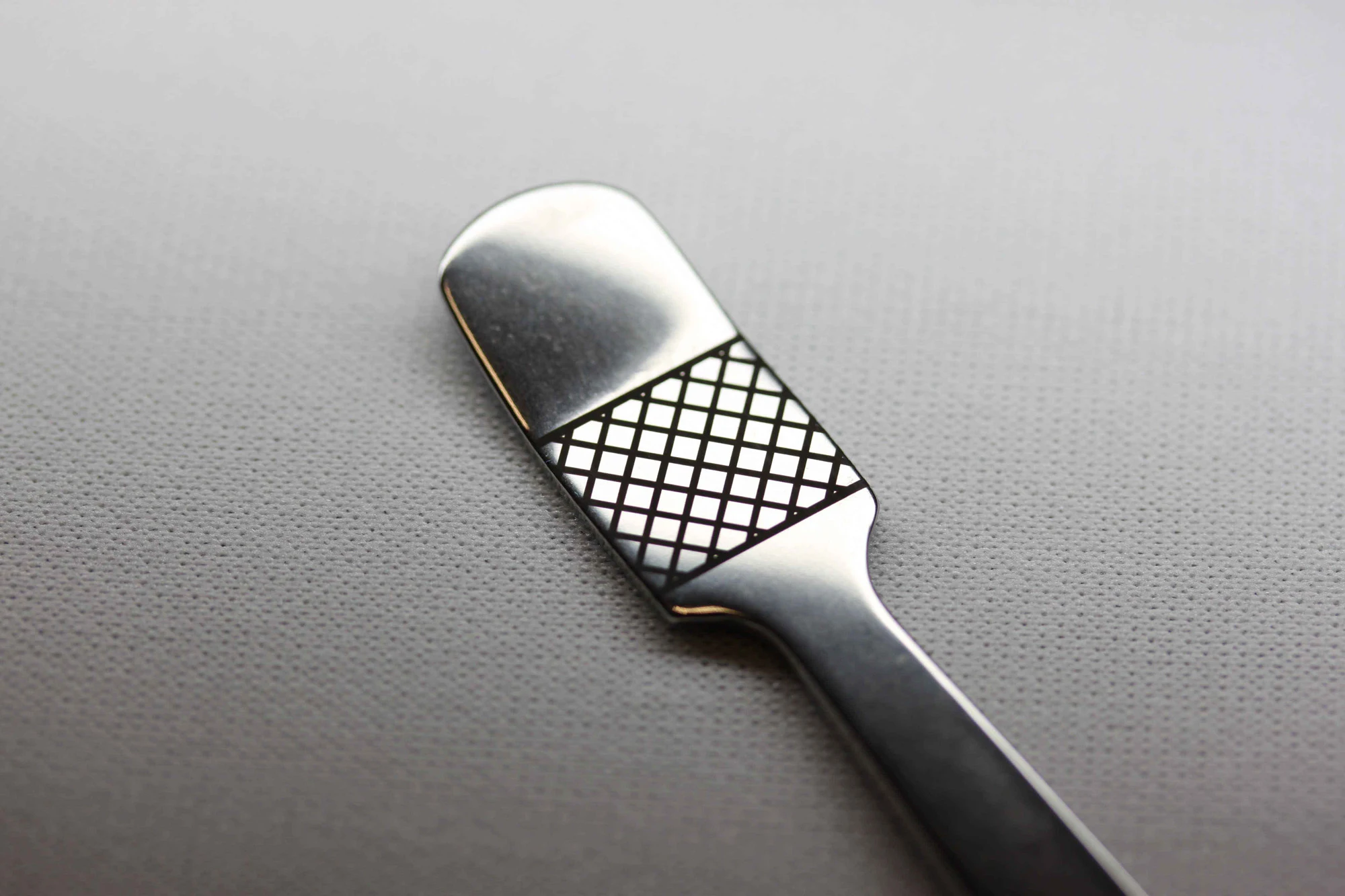
BENEFITS OF BLACK MARKING
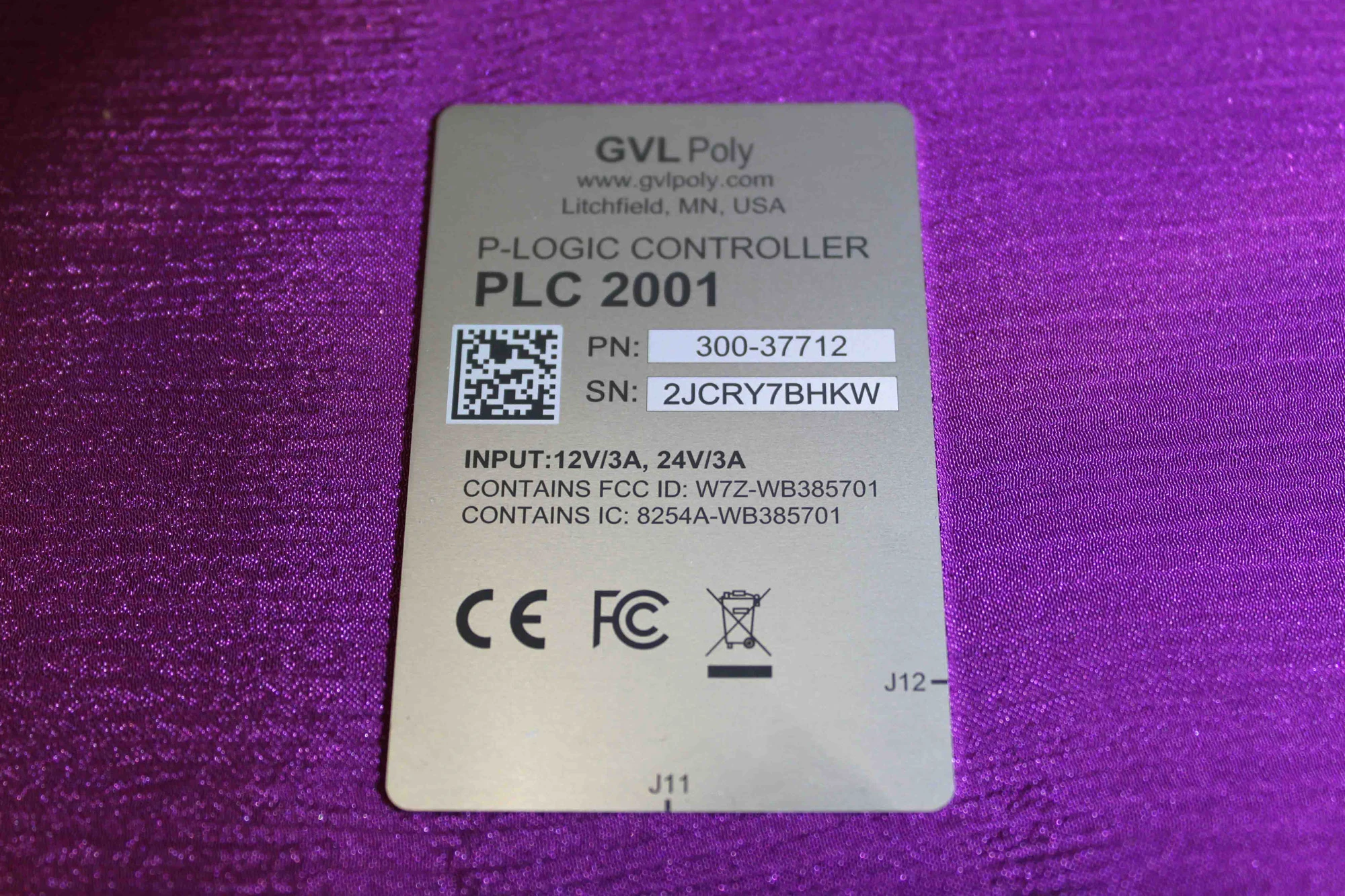
- Durable
- High Contrast
- Corrosion resistant
- Can eliminate the need for chemical passivation after marking
- Parts can withstand hundreds of autoclave cycles
- Marking is more black than traditional laser marking
- Marking appears darker when ambient light reflects off material surface
- Marking is easier for barcode reader to read
- Marking produces better barcode verification results
- Produces long term readability as UDI’s
- Can mark very small lines at around .0012” wide (.030mm or 30 microns)
WHAT MAKES STEEL CORROSION RESISTANT
In stainless steel, the Chromium together with oxygen from the atmosphere build a thin protective oxide layer (passive layer) on the surface of the stainless steel that is a few nanometers thick. The chromium / iron ratio in the stainless is an indicator of the quality of the passive layer. Typical ns (nanosecond) laser marking requires a chemical passivation of the parts after marking to restore the passive layer. This is because during the ns laser marking process the chromium enriched passive layer is damaged and the iron in the marking area is deposited on the surface of the material. Vaporization, oxidation, heating, melting and ionization of the material by the laser beam can all remove chromium oxide thereby damaging the passive layer, which can lead to surface corrosion of the stainless steel.
With Ultrafast or Black Laser Marking, the process is non-thermal in nature and does not melt or recast the material or deposit iron on the material surface.
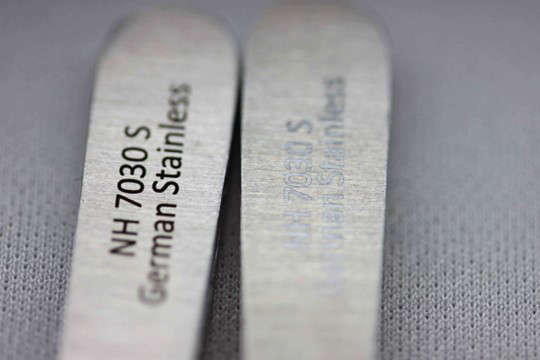
Above: On the left you see ambient light reflecting off a Black Marked Stainless Instrument Handle. On the right you see the same light reflecting off an identical Instrument that was laser marked using a traditional or ns laser marking process.
ADDITIONAL INFORMATION
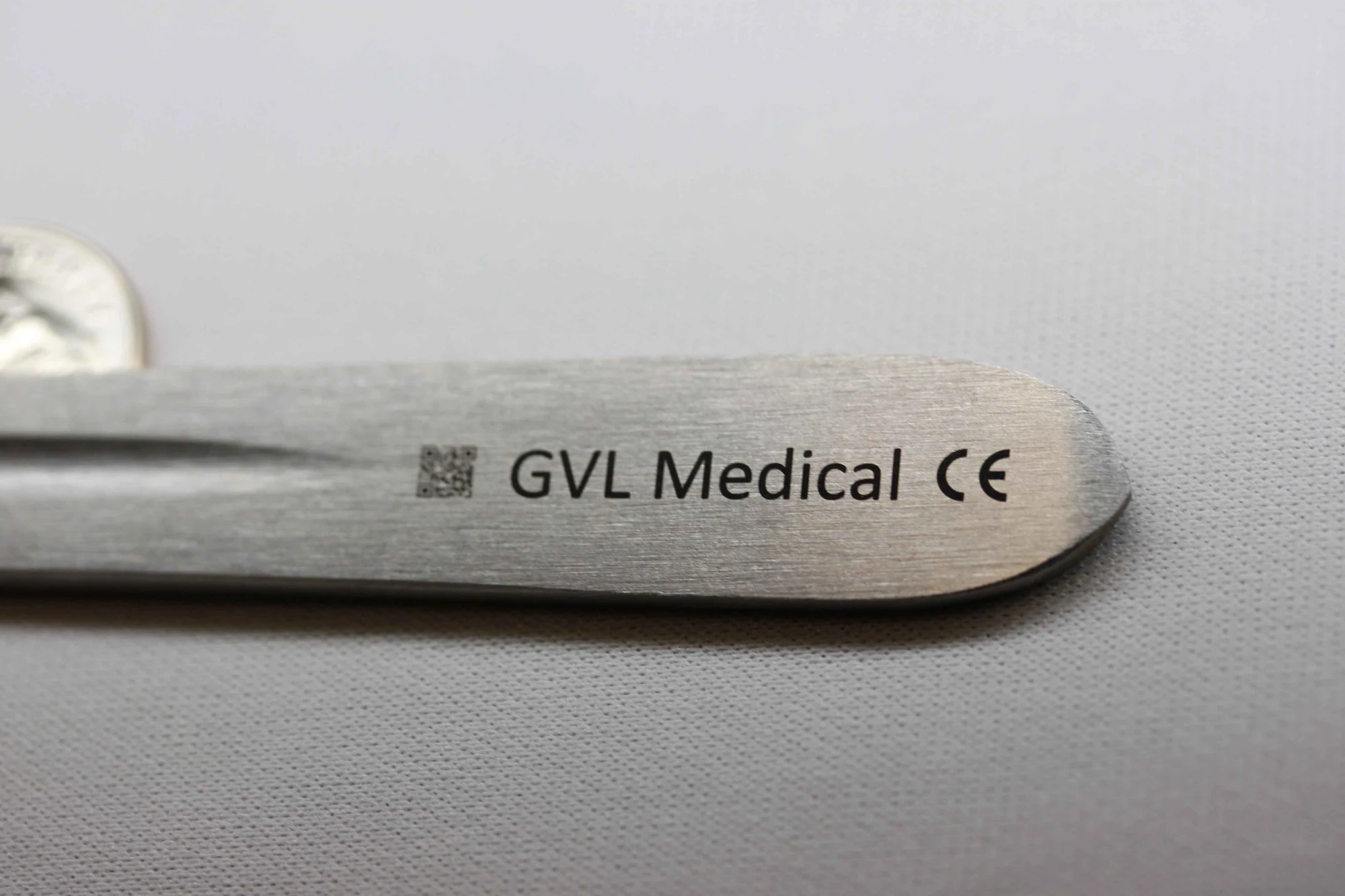
EDX (Energy-dispersive X-ray spectroscopy) tests have shown that Black Marked areas of stainless steel have a thin oxide layer present, indicating that the protective passive layer is still intact.
Marked austenitic steel (300 series stainless steels) typically show better corrosion resistance than martensitic steel (400 series stainless steels) when marked with Black Marking technology.
Black marking creates LIPSS – Laser induced periodic surface structures that act as a light trap making the laser marked areas appear quite black in color.
Verification of corrosion resistance can be done by an accredited lab such as Niutec.
With the proper set up, no secondary passivation is needed for medical parts that have been marked with Black Marking technology.
There is minimal heat input to the part and virtually no HAZ or thermal stress to the material due to the ultra-short laser pulses used in processing.
Due to its high carbon content, AISI 440B doesn’t have the same corrosion resistance following Black Marking that many of the other stainless steels have.
A 5% NaCl bath can test for corrosion resistance in many instances.
Another corrosion test is the F – ASTM A697/A697M-13 free iron test.
Yet another corrosion test can be found in the DIN EN ISO 13402 standard.